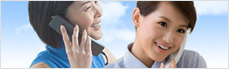
电话:86-0511-86389378
传真:86-0511-86382256
联系人:严国峰
手机:13914586636
网址 :http://www.jshangfeng.com
揭秘压铸加工中的五大常见误区!90%的企业还在踩坑?
压铸加工是制造业中广泛应用的核心工艺,从汽车零件到电子设备外壳,它的效率和质量直接影响着企业利润。但看似成熟的压铸技术背后,许多企业却因为一些“隐形误区”付出了高昂代价——废品率居高不下、模具寿命缩短、生产成本失控……今天我们就来扒一扒压铸行业常见的五大误区,看看你是否也在踩坑!
误区一:盲目追求“低成本材料”
“材料能用就行,选便宜的!”——这是很多老板的惯性思维。殊不知,材料选择不当会导致压铸件出现气孔、裂纹甚至批量报废。
典型案例:某中型压铸厂为节省成本,采购了杂质含量超标的铝合金锭,结果生产出的零件在后期热处理时大面积开裂,直接损失超50万元。
解决方案:
根据产品用途选择国标材料(如ADC12、A380等),优先与正规供应商合作;
对每批次原材料做成分检测,避免杂质超标;
特殊场景下可考虑“再生铝+新铝”的科学配比,平衡成本与性能。
误区二:模具“能用就行”,维护全靠运气
“模具没坏就不用管!”这种心态堪称压铸厂的“慢性毒药”。模具的精度和温度控制直接影响产品尺寸稳定性,而疏于保养的模具轻则导致毛刺增多,重则引发粘模、龟裂等致命问题。
血的教训:某企业因未及时清理模具排气槽,导致压铸过程中气体无法排出,连续3批产品出现气孔缺陷,客户直接取消订单。
正确操作:
每5000模次后对模具进行深度清洗和氮化处理;
每日检查模具冷却水道是否堵塞;
采用“模温机+离型剂喷涂系统”精准控制模具温度。
误区三:工艺参数“调一次就一劳永逸”
“参数调好了就不用动了?”大错特错!压铸机的压力、速度、温度等参数需要根据材料特性、环境温度甚至设备磨损动态调整。
真实案例:某工厂夏季未调整压射速度,铝液在高温下流动性变差,导致薄壁件填充不足,废品率飙升20%。
科学方法:
建立“工艺参数数据库”,针对不同产品、季节设定参数范围;
利用物联网传感器实时监控设备状态,自动优化参数;
定期对压铸机进行精度校准(尤其是锁模力)。
误区四:只盯“生产效率”,忽视质量管控
“多开模、多出货就能多赚钱?”这种盲目追求产量的做法,反而会让企业陷入“生产越多,赔得越狠”的怪圈。压铸件的内部缺陷(如缩松、冷隔)往往在后期装配或使用中才会暴露,一旦流入市场可能面临巨额索赔。
避坑指南:
关键工序设置全检点(如首件检验、每2小时抽检);
引入X射线探伤机、光谱仪等设备检测内部缺陷;
对质检员进行AI图像识别培训,提升缺陷检出率。
误区五:车间环境“差不多就行”
“车间脏点乱点不影响生产?”真相是——压铸对湿度、粉尘、温度极其敏感!空气中漂浮的金属粉尘可能混入铝液,湿度过高会导致铸件表面气泡,而温度波动则会影响合金结晶效果。
升级建议:
安装工业除湿机和空气净化系统,湿度控制在40%-60%;
严格区分熔炼区、压铸区和后处理区,避免交叉污染;
地面铺设防静电环氧地坪,减少杂质吸附。
结语:避开误区=捡钱!
压铸加工看似粗放,实则是一门需要“较真”的技术。从材料、模具到车间环境,每一个细节都藏着利润空间。那些抱怨“行业卷不动”的企业,不妨回头看看:是否还在用十年前的老方法?是否忽略了这些看似不起眼的“隐形成本”?
记住——压铸行业的竞争,早已从“拼规模”转向“拼细节”。避开这五大误区,下一个实现“废品率减半、利润翻倍”的可能就是你!